Page 38 from: Recycling International Jan/Feb 2025
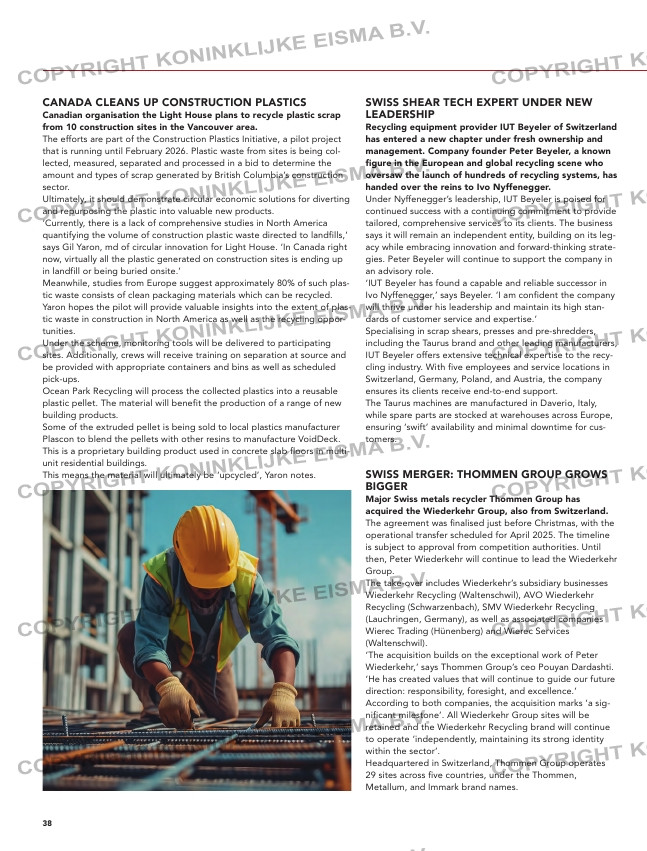
38
RESEARCHERS PLOT PATH TO UK’S FIRST WETSUIT
RECYCLING FACILITY
A plan to develop the UK’s first wetsuit recycling facility is among
eight new projects being considered in a collaboration between five
universities and the UK Fashion and Textile Association (UKFT).
The projects are being funded by a £1 million (EUR 1.2 million) pot from
Future Fibres Network Plus which aims to bring environmental science
into the heart of the UK fashion, clothing and textile sectors.
Many wetsuits are made from neoprene but the UK currently has no
way of recycling them, meaning more than 380 tonnes is burned or
landfilled each year. Led by the University of Plymouth and working with
industry partner Circular Flow, the project will examine the scope for
developing a UK neoprene recycling facility.
Dr Kayleigh Wyles, associate professor in environmental psychology at
the University of Plymouth and project lead, says: ‘Our project will
investigate the level of interest among UK businesses for returning end-
of-life wetsuits and accessories to a UK facility where they can be
turned into new and useful products.’
‘We also aim to understand consumers’ willingness to purchase and
wear recycled neoprene products and explore the logistics of develop-
ing a recycling facility.”
Circular Flow already has a facility in Bulgaria but one in the UK would
be seen as a significant development.
PROGRESS ON BELFAST RARE EARTH INITIATIVE
Plans for a magnet recycling facility in Northern Ireland have
advanced with the completion of a feasibility study.
Project Ionic Rare Earth Recycling encompasses the design and
construction of a new magnet recycling plant on an existing brown-
field site in Belfast for Ionic Technologies.
The study was carried out by consultancy and provides a more
refined cost estimate and incorporates design improvements while
prioritising operational health and safety. It covered a range of ser-
vices including design management, process engineering, mechani-
cal and electrical, architectural, and civil and structural engineering.
WSP also provided environmental consultancy support to Ionic
Technologies.
China accounts for 87% of the production of magnet rare earth
oxides while its downstream capabilities account for nearly 95% of
global permanent magnet manufacturing. Ionic Technologies’ goal
is for a more sustainable future by extracting and recycling rare
earth oxides (REO) from end-of-life magnets.
Tim Harrison, md, IonicRE, says the completion of the feasibility
study is a significant milestone in the development of a western
rare earths supply chain, initially centred on Belfast. ‘Significantly,
the study confirms that the commercial case for magnet recycling is
compelling, complementing the clear environmental and sustain-
ability benefits, as well as the growing requirement for REO produc-
tion outside of China.’
Andrew Woodward, Head of Industry at WSP, says: ‘Rare earths are
critical to the future of the Net Zero energy transition, and this mile-
stone reflects our shared commitment to designing for a sustain-
able future and achieving net zero together.’
CANADA CLEANS UP CONSTRUCTION PLASTICS
Canadian organisation the Light House plans to recycle plastic scrap
from 10 construction sites in the Vancouver area.
The efforts are part of the Construction Plastics Initiative, a pilot project
that is running until February 2026. Plastic waste from sites is being col-
lected, measured, separated and processed in a bid to determine the
amount and types of scrap generated by British Columbia’s construction
sector.
Ultimately, it should demonstrate circular economic solutions for diverting
and repurposing the plastic into valuable new products.
‘Currently, there is a lack of comprehensive studies in North America
quantifying the volume of construction plastic waste directed to landfills,’
says Gil Yaron, md of circular innovation for Light House. ‘In Canada right
now, virtually all the plastic generated on construction sites is ending up
in landfill or being buried onsite.’
Meanwhile, studies from Europe suggest approximately 80% of such plas-
tic waste consists of clean packaging materials which can be recycled.
Yaron hopes the pilot will provide valuable insights into the extent of plas-
tic waste in construction in North America as well as the recycling oppor-
tunities.
Under the scheme, monitoring tools will be delivered to participating
sites. Additionally, crews will receive training on separation at source and
be provided with appropriate containers and bins as well as scheduled
pick-ups.
Ocean Park Recycling will process the collected plastics into a reusable
plastic pellet. The material will benefit the production of a range of new
building products.
Some of the extruded pellet is being sold to local plastics manufacturer
Plascon to blend the pellets with other resins to manufacture VoidDeck.
This is a proprietary building product used in concrete slab floors in multi-
unit residential buildings.
This means the material will ultimately be ‘upcycled’, Yaron notes.
SWISS SHEAR TECH EXPERT UNDER NEW
LEADERSHIP
Recycling equipment provider IUT Beyeler of Switzerland
has entered a new chapter under fresh ownership and
management. Company founder Peter Beyeler, a known
figure in the European and global recycling scene who
oversaw the launch of hundreds of recycling systems, has
handed over the reins to Ivo Nyffenegger.
Under Nyffenegger’s leadership, IUT Beyeler is poised for
continued success with a continuing commitment to provide
tailored, comprehensive services to its clients. The business
says it will remain an independent entity, building on its leg-
acy while embracing innovation and forward-thinking strate-
gies. Peter Beyeler will continue to support the company in
an advisory role.
‘IUT Beyeler has found a capable and reliable successor in
Ivo Nyffenegger,’ says Beyeler. ‘I am confident the company
will thrive under his leadership and maintain its high stan-
dards of customer service and expertise.’
Specialising in scrap shears, presses and pre-shredders,
including the Taurus brand and other leading manufacturers,
IUT Beyeler offers extensive technical expertise to the recy-
cling industry. With five employees and service locations in
Switzerland, Germany, Poland, and Austria, the company
ensures its clients receive end-to-end support.
The Taurus machines are manufactured in Daverio, Italy,
while spare parts are stocked at warehouses across Europe,
ensuring ‘swift’ availability and minimal downtime for cus-
tomers.
SWISS MERGER: THOMMEN GROUP GROWS
BIGGER
Major Swiss metals recycler Thommen Group has
acquired the Wiederkehr Group, also from Switzerland.
The agreement was finalised just before Christmas, with the
operational transfer scheduled for April 2025. The timeline
is subject to approval from competition authorities. Until
then, Peter Wiederkehr will continue to lead the Wiederkehr
Group.
The take-over includes Wiederkehr’s subsidiary businesses
Wiederkehr Recycling (Waltenschwil), AVO Wiederkehr
Recycling (Schwarzenbach), SMV Wiederkehr Recycling
(Lauchringen, Germany), as well as associated companies
Wierec Trading (Hünenberg) and Wierec Services
(Waltenschwil).
‘The acquisition builds on the exceptional work of Peter
Wiederkehr,’ says Thommen Group’s ceo Pouyan Dardashti.
‘He has created values that will continue to guide our future
direction: responsibility, foresight, and excellence.’
According to both companies, the acquisition marks ‘a sig-
nificant milestone’. All Wiederkehr Group sites will be
retained and the Wiederkehr Recycling brand will continue
to operate ‘independently, maintaining its strong identity
within the sector’.
Headquartered in Switzerland, Thommen Group operates
29 sites across five countries, under the Thommen,
Metallum, and Immark brand names.
36-37-38-39-40_trendsupdates214paginaadv.indd 38 29-01-2025 16:29