Page 37 from: Recycling International Jan/Feb 2025
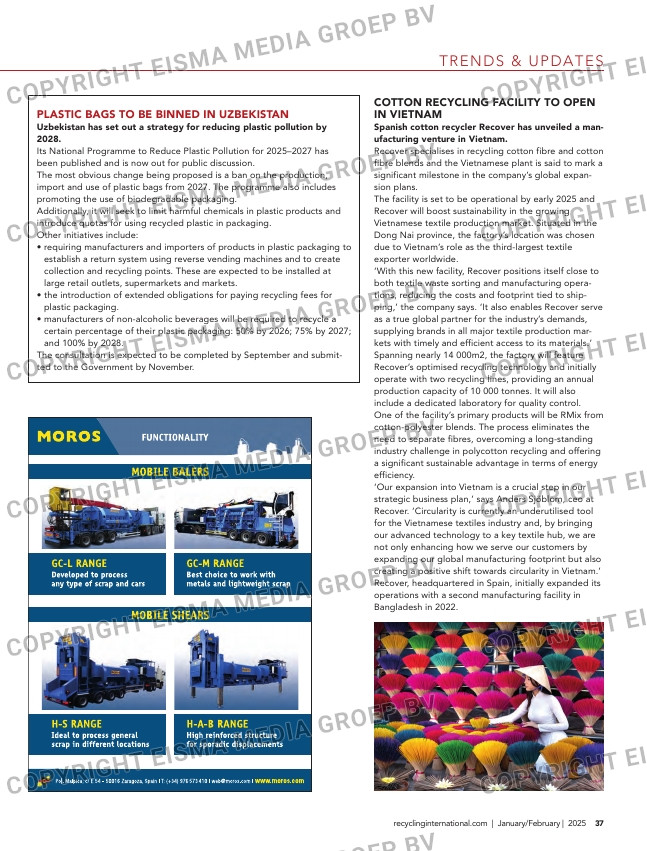
TRENDS & UPDATES
37recyclinginternational.com | January/February | 2025
Fotobijschrift
PACKAGING MAJOR ‘ON TRACK’ TO DOUBLE RECYCLING
It’s the time of the year big companies present their annual results and global packaging and recycling specialist Alpla is no excep-
tion. In 2024 its turnover increased by EUR 200 million to EUR 4.9 billion. What’s more, the company claims to be well on the way
to boost recycling capacity. By 2030, it aims to double its annual recycling output to 700 000 tonnes.
Alpla has made recycling a cornerstone of its growth strategy. The company operates 13 recycling plants in nine countries, producing
recycled PET and recycled HDPE. With an annual investment of EUR 50 million in recycling infrastructure, the company is ‘on track’ to
achieve its short-term target of incorporating 25% recycled material into its packaging this year.
‘We’re not just meeting demand for sustainable materials, we’re driving innovation in recycling to reduce carbon footprints and ensure
recyclability,’ comments company ceo Philipp Lehner. The strategy includes light packaging and designing products specifically for recy-
cling, ‘further optimising material use and sustainability’.
In 2024 Alpla launched new locations and now has 200 production plants
worldwide. Plans for a new plant in Thailand in 2025 will boost the compa-
ny’s presence in the Asia-Pacific region, a market with ‘significant’ poten-
tial.
In Europe, Alpla is addressing ever-strict regulation regimes with a focus on
efficiency and innovation. Meanwhile, growth markets in South America,
Africa, and the Middle East have shown ‘robust performance’, contributing
to the company’s overall expansion.
Alpla’s investments in recycling are not just about capacity, according to
Lehner: ‘They are
about leadership in sustainability.’ By integrating advanced recycling tech-
nologies and expanding global operations, the company wants to set the
standard for circular economy practices in the packaging industry.
COTTON RECYCLING FACILITY TO OPEN
IN VIETNAM
Spanish cotton recycler Recover has unveiled a man-
ufacturing venture in Vietnam.
Recover specialises in recycling cotton fibre and cotton
fibre blends and the Vietnamese plant is said to mark a
significant milestone in the company’s global expan-
sion plans.
The facility is set to be operational by early 2025 and
Recover will boost sustainability in the growing
Vietnamese textile production market. Situated in the
Dong Nai province, the factory’s location was chosen
due to Vietnam’s role as the third-largest textile
exporter worldwide.
‘With this new facility, Recover positions itself close to
both textile waste sorting and manufacturing opera-
tions, reducing the costs and footprint tied to ship-
ping,’ the company says. ‘It also enables Recover serve
as a true global partner for the industry’s demands,
supplying brands in all major textile production mar-
kets with timely and efficient access to its materials.’
Spanning nearly 14 000m2, the factory will feature
Recover’s optimised recycling technology and initially
operate with two recycling lines, providing an annual
production capacity of 10 000 tonnes. It will also
include a dedicated laboratory for quality control.
One of the facility’s primary products will be RMix from
cotton-polyester blends. The process eliminates the
need to separate fibres, overcoming a long-standing
industry challenge in polycotton recycling and offering
a significant sustainable advantage in terms of energy
efficiency.
‘Our expansion into Vietnam is a crucial step in our
strategic business plan,’ says Anders Sjöblom, ceo at
Recover. ‘Circularity is currently an underutilised tool
for the Vietnamese textiles industry and, by bringing
our advanced technology to a key textile hub, we are
not only enhancing how we serve our customers by
expanding our global manufacturing footprint but also
creating a positive shift towards circularity in Vietnam.’
Recover, headquartered in Spain, initially expanded its
operations with a second manufacturing facility in
Bangladesh in 2022.
PLASTIC BAGS TO BE BINNED IN UZBEKISTAN
Uzbekistan has set out a strategy for reducing plastic pollution by
2028.
Its National Programme to Reduce Plastic Pollution for 2025–2027 has
been published and is now out for public discussion.
The most obvious change being proposed is a ban on the production,
import and use of plastic bags from 2027. The programme also includes
promoting the use of biodegradable packaging.
Additionally, it will seek to limit harmful chemicals in plastic products and
introduce quotas for using recycled plastic in packaging.
Other initiatives include:
• requiring manufacturers and importers of products in plastic packaging to
establish a return system using reverse vending machines and to create
collection and recycling points. These are expected to be installed at
large retail outlets, supermarkets and markets.
• the introduction of extended obligations for paying recycling fees for
plastic packaging.
• manufacturers of non-alcoholic beverages will be required to recycle a
certain percentage of their plastic packaging: 50% by 2026; 75% by 2027;
and 100% by 2028.
The consultation is expected to be completed by September and submit-
ted to the Government by November.
PETCORE SETS OUT ROADMAP FOR CIRCULAR POLYESTER TEXTILES
Improved collection, mandatory harmonised sorting and a pre-processing infrastructure are essential for the circularity of poly-
ester textiles, insists leading members of the PET value chain in Europe.
Petcore Europe, the association covering the PET lifecycle from manu-
facturing to conversion into packaging, has published a position paper
on the EU’s Ecodesign for Sustainable Products Regulation (ESPR) which
came into force in July 2024.
The organisation says post-consumer garments in the EU represent 85%
of textiles waste and they should be designed with recyclability in mind.
‘We stress the pressing need to improve collection efforts, establish
mandatory EU-wide harmonised sorting guidelines, implementation of
the pre-processing infrastructure to convert collected textile waste to
consistent usable feedstock both, mechanical recycling and depolymeri-
sation processes,’ says Petcore.
‘ These critical measures are vital for securing the viability of recycling
facilities, ensuring the industry can achieve the ambitious targets set by
the ESPR Ecodesign framework.’
It argues that the economic and social impact of textile recycling is undeniable, generating employment, supporting local industries
and, ultimately, becoming economically self-sustaining.
Noting the need for extended producer responsibility schemes, Petcore says key elements include ensuring accountability for waste
prevention, reuse and recycling targets. ‘These schemes must provide financial support for the collection, sorting, preparation for
recycling, and recycling.’
It advocates a mandatory minimum of 20% recycled content in garments, specifically post-consumer recycled polyester, by 2030. It
also supports an initiative for digital product passports for polyester textiles that provide meaningful information on a product’s envi-
ronmental footprint, composition, repairability, and recyclability.
Additionally, ‘We support mandating producer responsibility for garment take-back schemes and ensuring proper traceability for
upcycling.’ The position paper calls for a reduction on textile exports to the Global South: ‘A firm ban on the export of unsorted
clothing is essential.’
36-37-38-39-40_trendsupdates214paginaadv.indd 37 29-01-2025 16:29