Page 34 from: Recycling International Jan/Feb 2025
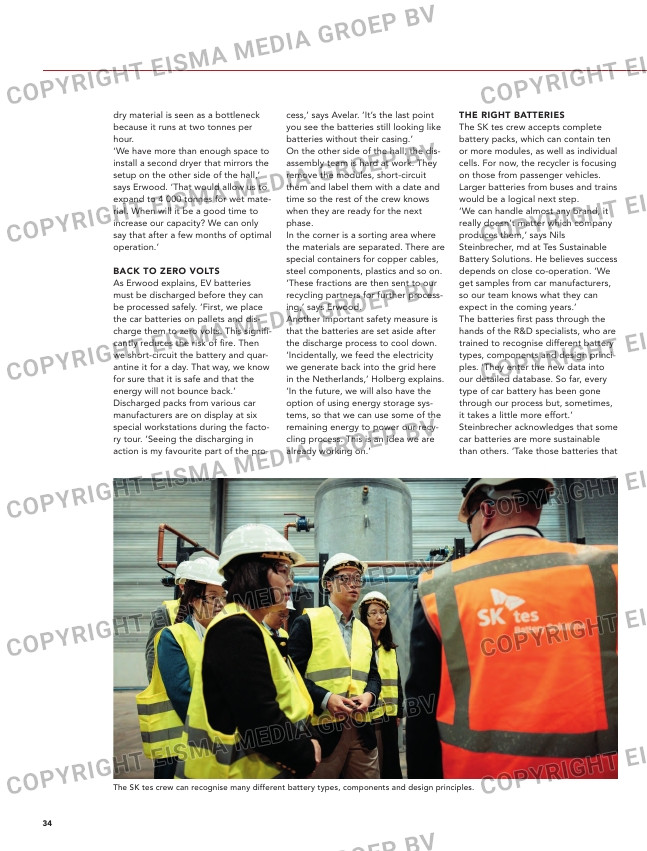
34
are glued into the packaging, for
example. It makes dismantling unnec-
essarily difficult. It’s really annoying
for recyclers. I don’t understand why
a car manufacturer would do that.
Who stands to benefit?’
TAMING THE FLAMES
As the journalists leave the site, we
pass a dozen sea containers. ‘Inside,
we store charged batteries that we
still have to process,’ Erwood
explains. ‘Each container holds about
ten tonnes of batteries.’ They are
kept as far from each other as possi-
ble for safety reasons; they could
spontaneously ignite and cause a fire.
‘We make sure nothing is within ten
metres of the containers, only empty
space. This measure is based on a
Dutch safety law.’
SK tes’ containers are equipped with
smoke and carbon monoxide detec-
tors as well as temperature sensors
which sound the alarm at crucial
thresholds. ‘These alerts are immedi-
ately forwarded to the local fire bri-
gade, which is fortunately only three
dry material is seen as a bottleneck
because it runs at two tonnes per
hour.
‘We have more than enough space to
install a second dryer that mirrors the
setup on the other side of the hall,’
says Erwood. ‘That would allow us to
expand to 4 000 tonnes for wet mate-
rial. When will it be a good time to
increase our capacity? We can only
say that after a few months of optimal
operation.’
BACK TO ZERO VOLTS
As Erwood explains, EV batteries
must be discharged before they can
be processed safely. ‘First, we place
the car batteries on pallets and dis-
charge them to zero volts. This signifi-
cantly reduces the risk of fire. Then
we short-circuit the battery and quar-
antine it for a day. That way, we know
for sure that it is safe and that the
energy will not bounce back.’
Discharged packs from various car
manufacturers are on display at six
special workstations during the facto-
ry tour. ‘Seeing the discharging in
action is my favourite part of the pro-
cess,’ says Avelar. ‘It’s the last point
you see the batteries still looking like
batteries without their casing.’
On the other side of the hall, the dis-
assembly team is hard at work. They
remove the modules, short-circuit
them and label them with a date and
time so the rest of the crew knows
when they are ready for the next
phase.
In the corner is a sorting area where
the materials are separated. There are
special containers for copper cables,
steel components, plastics and so on.
‘These fractions are then sent to our
recycling partners for further process-
ing,’ says Erwood.
Another important safety measure is
that the batteries are set aside after
the discharge process to cool down.
‘Incidentally, we feed the electricity
we generate back into the grid here
in the Netherlands,’ Holberg explains.
‘In the future, we will also have the
option of using energy storage sys-
tems, so that we can use some of the
remaining energy to power our recy-
cling process. This is an idea we are
already working on.’
THE RIGHT BATTERIES
The SK tes crew accepts complete
battery packs, which can contain ten
or more modules, as well as individual
cells. For now, the recycler is focusing
on those from passenger vehicles.
Larger batteries from buses and trains
would be a logical next step.
‘We can handle almost any brand, it
really doesn’t matter which company
produces them,’ says Nils
Steinbrecher, md at Tes Sustainable
Battery Solutions. He believes success
depends on close co-operation. ‘We
get samples from car manufacturers,
so our team knows what they can
expect in the coming years.’
The batteries first pass through the
hands of the R&D specialists, who are
trained to recognise different battery
types, components and design princi-
ples. ‘They enter the new data into
our detailed database. So far, every
type of car battery has been gone
through our process but, sometimes,
it takes a little more effort.’
Steinbrecher acknowledges that some
car batteries are more sustainable
than others. ‘Take those batteries that
The SK tes crew can recognise many different battery types, components and design principles. SK tes has teamed up with BMW to ensure its EV batteries get recycled.
32-33-34-35_sktes.indd 34 29-01-2025 11:27