Page 30 from: Recycling International Jan/Feb 2025
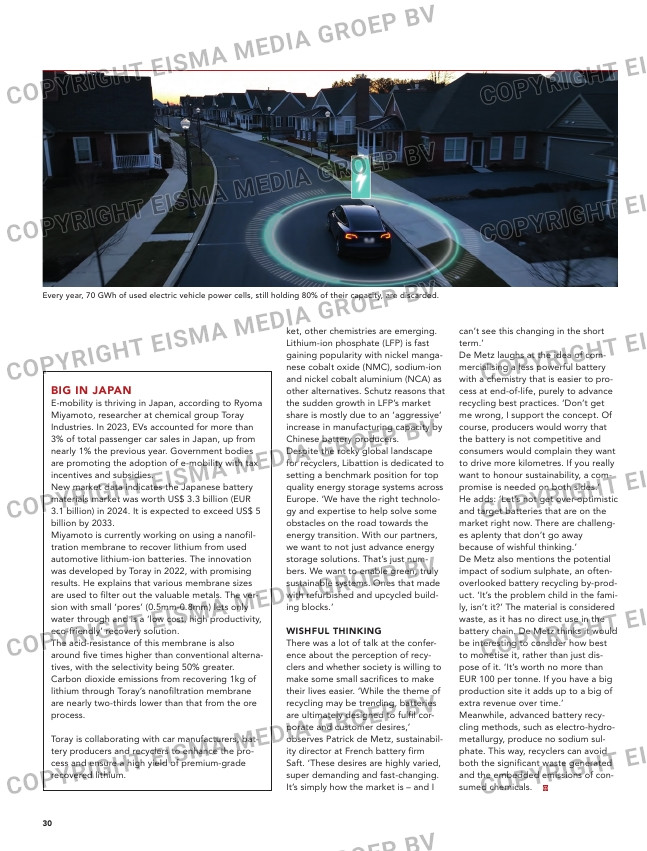
30
ket, other chemistries are emerging.
Lithium-ion phosphate (LFP) is fast
gaining popularity with nickel manga-
nese cobalt oxide (NMC), sodium-ion
and nickel cobalt aluminium (NCA) as
other alternatives. Schutz reasons that
the sudden growth in LFP’s market
share is mostly due to an ‘aggressive’
increase in manufacturing capacity by
Chinese battery producers.
Despite the rocky global landscape
for recyclers, Libattion is dedicated to
setting a benchmark position for top
quality energy storage systems across
Europe. ‘We have the right technolo-
gy and expertise to help solve some
obstacles on the road towards the
energy transition. With our partners,
we want to not just advance energy
storage solutions. That’s just num-
bers. We want to enable green, truly
sustainable systems. Ones that made
with refurbished and upcycled build-
ing blocks.’
WISHFUL THINKING
There was a lot of talk at the confer-
ence about the perception of recy-
clers and whether society is willing to
make some small sacrifices to make
their lives easier. ‘While the theme of
recycling may be trending, batteries
are ultimately designed to fulfil cor-
porate and customer desires,’
observes Patrick de Metz, sustainabil-
ity director at French battery firm
Saft. ‘These desires are highly varied,
super demanding and fast-changing.
It’s simply how the market is – and I
can’t see this changing in the short
term.’
De Metz laughs at the idea of com-
mercialising a less powerful battery
with a chemistry that is easier to pro-
cess at end-of-life, purely to advance
recycling best practices. ‘Don’t get
me wrong, I support the concept. Of
course, producers would worry that
the battery is not competitive and
consumers would complain they want
to drive more kilometres. If you really
want to honour sustainability, a com-
promise is needed on both sides.’
He adds: ‘Let’s not get over-optimistic
and target batteries that are on the
market right now. There are challeng-
es aplenty that don’t go away
because of wishful thinking.’
De Metz also mentions the potential
impact of sodium sulphate, an often-
overlooked battery recycling by-prod-
uct. ‘It’s the problem child in the fami-
ly, isn’t it?’ The material is considered
waste, as it has no direct use in the
battery chain. De Metz thinks it would
be interesting to consider how best
to monetise it, rather than just dis-
pose of it. ‘It’s worth no more than
EUR 100 per tonne. If you have a big
production site it adds up to a big of
extra revenue over time.’
Meanwhile, advanced battery recy-
cling methods, such as electro-hydro-
metallurgy, produce no sodium sul-
phate. This way, recyclers can avoid
both the significant waste generated
and the embedded emissions of con-
sumed chemicals.
BIG IN JAPAN
E-mobility is thriving in Japan, according to Ryoma
Miyamoto, researcher at chemical group Toray
Industries. In 2023, EVs accounted for more than
3% of total passenger car sales in Japan, up from
nearly 1% the previous year. Government bodies
are promoting the adoption of e-mobility with tax
incentives and subsidies.
New market data indicates the Japanese battery
materials market was worth US$ 3.3 billion (EUR
3.1 billion) in 2024. It is expected to exceed US$ 5
billion by 2033.
Miyamoto is currently working on using a nanofil-
tration membrane to recover lithium from used
automotive lithium-ion batteries. The innovation
was developed by Toray in 2022, with promising
results. He explains that various membrane sizes
are used to filter out the valuable metals. The ver-
sion with small ‘pores’ (0.5mm-0.8mm) lets only
water through and is a ‘low cost, high productivity,
eco-friendly’ recovery solution.
The acid-resistance of this membrane is also
around five times higher than conventional alterna-
tives, with the selectivity being 50% greater.
Carbon dioxide emissions from recovering 1kg of
lithium through Toray’s nanofiltration membrane
are nearly two-thirds lower than that from the ore
process.
Toray is collaborating with car manufacturers, bat-
tery producers and recyclers to enhance the pro-
cess and ensure a high yield of premium-grade
recovered lithium.
Every year, 70 GWh of used electric vehicle power cells, still holding 80% of their capacity, are discarded.
28-29-30_batteryupdatepart2.indd 30 29-01-2025 11:26